If you are in the market for a metal roofing system, there are multiple metal material options available, such as steel, aluminum, copper, zinc, galvanized, and others, for you to choose from.
Aluminum is a frequently used metal roofing material in coastal areas due to its resistance to saltwater corrosion, and though it may not be as popular as steel (Galvalume), it is still widely utilized. How familiar are you with the key benefits and drawbacks of aluminum as a roofing material?
At Metal Roofing Experts, we specialize in providing and installing painted/bare Galvalume and painted aluminum roofs for the architectural metal roofing industry. It’s crucial for you to make an informed decision as a buyer, so let’s explore the specific details of aluminum and determine whether it’s the right choice for your project.
In this article, we will discuss:
- What is aluminum
- Uses for aluminum metal roofing
- Advantages of aluminum metal roofing
- Disadvantages of aluminum metal roofing
What Is Aluminum?
Aluminum, the third most abundant element on Earth, is found in compounds like aluminum sulfates rather than in its metallic form in nature. It makes up over 8% of the Earth’s core mass and is present in almost all types of rocks, plants, and animals
Aluminum is a commonly utilized material in numerous industries, particularly for product manufacturing.
Transportation includes automotive, aerospace, and locomotive industries.
Containers and packaging refer to beverage cans and similar items.
Construction involves roofing materials, cladding, railings, and more.
Electronics and appliances encompass electrical wires, washers, dryers, and other similar products.
Uses for Aluminum Metal Roofing Systems
Let’s discuss the key characteristics and uses of aluminum in metal roofing.
Aluminum sheet and coil products are available in varying thicknesses, typically measured in inches as a decimal. The higher the number/decimal, the thicker the aluminum material. The thickness you should purchase depends on the specific application for which it will be used.
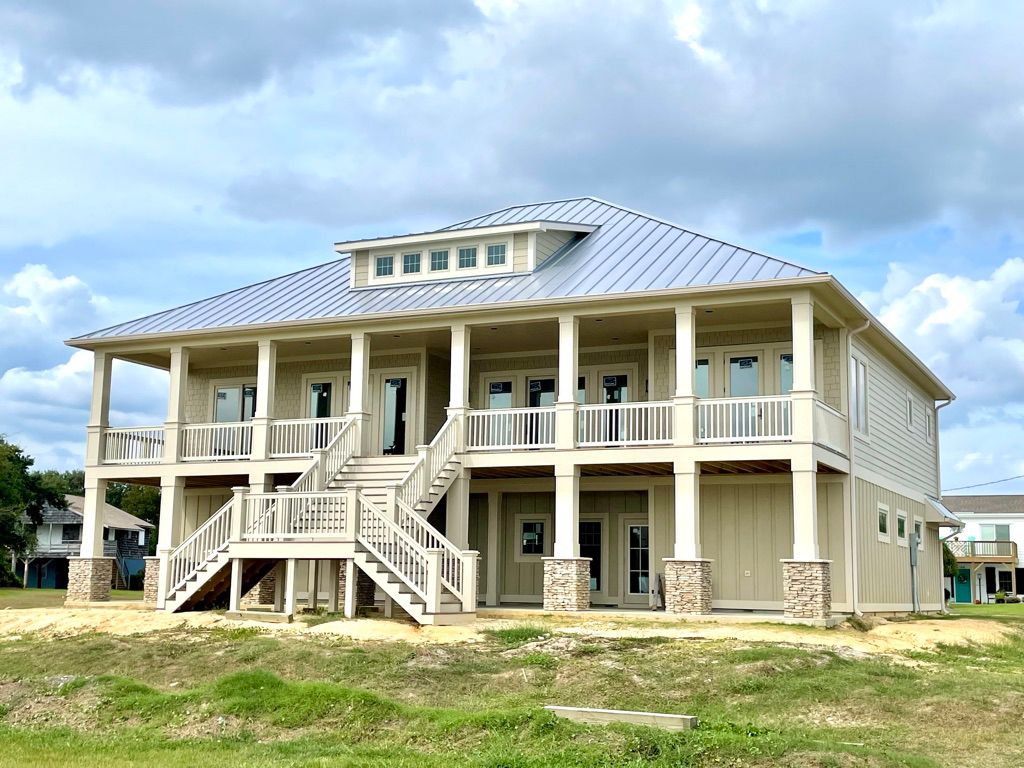
In residential roofing projects, the most common thickness for materials is .032” or .030”.
For commercial roofing projects, the most common thickness is .040”.
When it comes to copings or caps, .050” or .063” is most commonly used.
In various environments, including coastal areas, hurricane zones, and regions with high rain or snowfall, aluminum is suitable for use as a roof, wall, trim, and other applications. Additionally, it can withstand high temperatures and is a versatile material for a variety of purposes.
Some common uses for aluminum include
Coastal structures like hotels, condominiums, homes, and boathouses, as well as commercial buildings such as hospitals, schools, and stores, and residential projects including single-family and multi-family homes, and architectural structures like commercial, governmental, and residential buildings, are all examples of different types of buildings. Additionally, structural or industrial applications may include warehouses and factories.
Benefits of Aluminum Metal Roofing
Self Healing & No Red Rust
Aluminum has a unique way of handling corrosion, as it forms a protective oxide film when it corrodes, rather than red rust like steel. This oxide film helps to preserve the metal and make it last in corrosive environments, such as coastlines. Additionally, the oxidation forms quickly and prevents edge creep, which can deteriorate the panel like red rust does with steel.
Suitable For Use in Coastal Environments
Aluminum’s superior corrosion resistance makes it an ideal choice for installation in coastal environments. Unlike steel products, aluminum can withstand the harsh conditions of saltwater and oxidation, making it not only durable but also prolonging the life of the roofing system.
Aluminum is the most commonly installed metal material in the Caribbean Islands, as well as on the Atlantic coastline, the Gulf Coast, and the Pacific Coast. This is due to the presence of salt residue in the air, which can cause Galvalume and other steel products to rust.
Additionally, aluminum roofing systems maintain a PVDF paint warranty even when installed in coastal areas, making them an excellent choice for durability and longevity.
Warrantied Product
It is highly advisable to invest in a roofing product that comes with a warranty, given the significance of your roof. Fortunately, aluminum metal roofs offer a range of warranty options, such as paint, substrate, and weathertight warranties, to safeguard your investment and ensure long-lasting performance. It’s important to consult with the manufacturer for details on specific warranty types and timeframes.
Highly Recyclable
In the last 20 to 25 years, sustainability has become increasingly important in construction, leading to the rise of metal products. Metal, especially aluminum, is highly recyclable, making it one of the most sustainable materials in construction. In fact, approximately 95% of all aluminum roofing systems installed globally are made from previously recycled aluminum. Some metal manufacturers even use a 3000 series aluminum alloy (3105) primarily made from recycled materials, with very little pure aluminum.
Lightweight
Metal roofing is known for being lightweight, which can help to lessen the strain on a building’s structure. In particular, aluminum stands out as one of the lightest metal materials, making it a great option for reducing the overall weight on a building’s frame, especially when compared to steel products.
Just to provide some context, when comparing gauges and thickness on a weight-per-square-foot basis, 24-gauge Galvalume typically measures as .023” or .024” in thickness. The comparable aluminum thickness is .032” (equivalent to 24-gauge Galvalume in strength), so the aluminum is thicker but only half the weight. As a result, a typical 24-gauge Galvalume roof weighs anywhere from 1 to 1.5 pounds per square foot, while a .032 aluminum roof weighs less than .5 pounds per square foot.
The use of aluminum in panels makes it more convenient for contractors and installers to transport, handle, and place them on the roof deck. Additionally, when using a portable rollforming machine on-site, a lighter aluminum coil is easier to transport and puts less stress on the machine. It’s important to note that because aluminum is thicker, aluminum coils will have slightly less lineal footage.
Readily Available
Aluminum is widely available in the Earth’s crust and is often produced from recycled metals, making it a popular choice for manufacturers of metal sheet and coil products. Additionally, there are numerous experienced contractors who are knowledgeable in properly installing aluminum according to the manufacturer’s recommended installation guidelines.
Color Options
Aluminum sheet and coil products typically offer a wide range of color options, often matching or closely resembling those available for Galvalume. This means that when choosing an aluminum panel system for your project, you can rest assured that you won’t have to compromise on finding the right color.
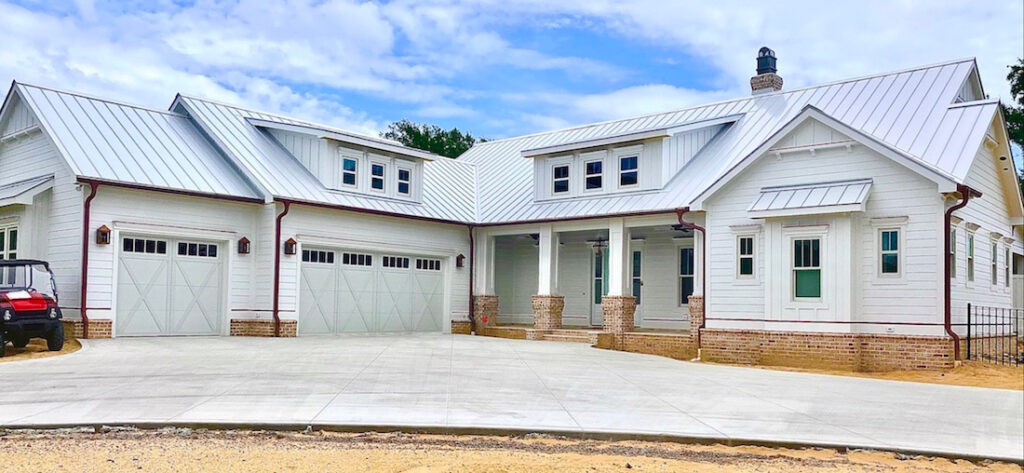
Drawbacks of Aluminum Metal Roofing
Easier to Bend or Dent
Aluminum’s malleability makes it easier to bend and manipulate, which is advantageous during rollforming and fabrication of panels. However, this same characteristic can also be a drawback, as aluminum is more susceptible to dents and dings compared to steel.
Aluminum is known for being softer and more malleable than other metals, which can make it more prone to denting during and after installation. It’s important for contractors to handle and install aluminum materials with extra care. In situations where a structure is at risk of objects falling onto the roof, it may be better to consider alternative metal materials to maintain the roof’s aesthetic.
Fortunately, aluminum has a tensile strength similar to that of steel, however, it is more prone to surface denting.
Medium to High Price Point
Aluminum standing seam metal roofs typically fall within the mid to high price range for material cost, with prices ranging from $7 to $18 per square foot. This cost can vary based on factors such as thickness, finish, profile, location, and installer. Overall, aluminum may not be the most affordable metal material option for roofing.
Requires More Space for Thermal Movement
Contractors should be mindful of the fact that aluminum expands and contracts approximately twice as much as a steel roof. This is crucial during installation to ensure there is enough space for the thermal movement of the panels. It is particularly important when using mechanically seamed panels longer than 15-20 feet, and it is recommended to use an expansion clip in accordance with the applicable engineering for panels of this length.
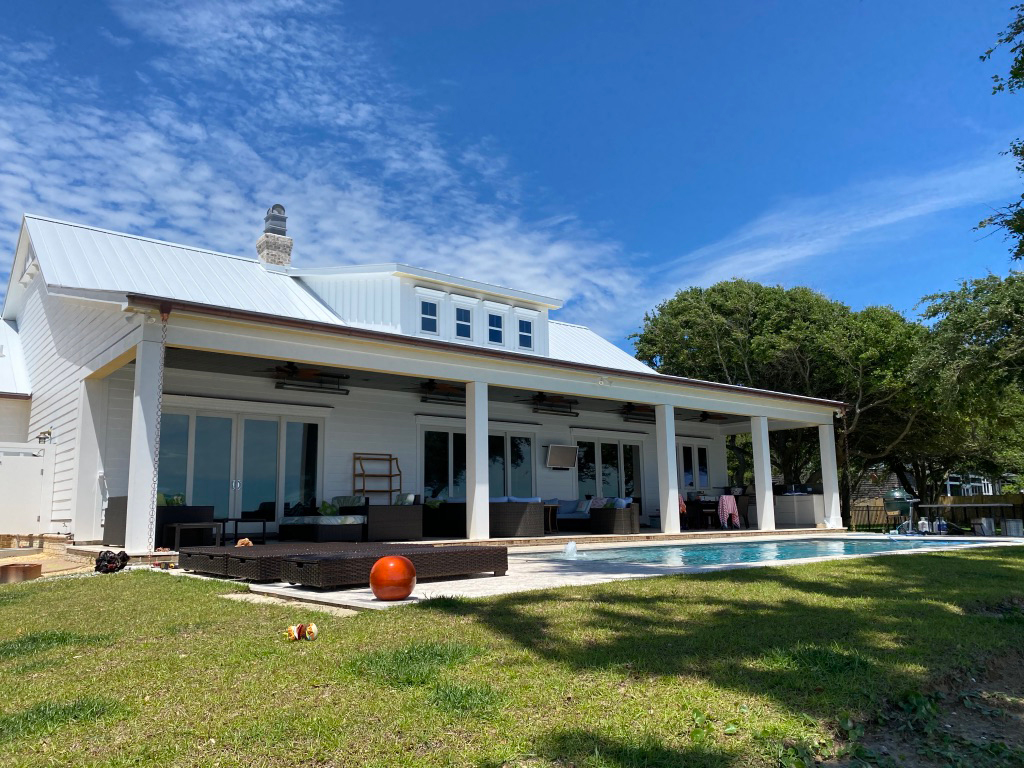
Limited thermal movement of an aluminum roof can lead to oil canning, heightened noise levels, and additional maintenance needs for exposed fasteners.
Natural Aluminum Color
It is generally not advised to use a bare aluminum product with its original natural silver-gray color. Over time, the metal will age, experience weathering, and oxidize, resulting in a loss of its original mill-finished color and often becoming washed out and spotty.
One effective solution for addressing this problem is to invest in painted roofing coils or panels. The paint coating will help maintain a cleaner appearance over time, as it will cover any natural metal color changes. .
Final Thoughts on Aluminum Metal Roofing
Aluminum is an excellent choice for roofing in many different scenarios, but it’s crucial to understand the specific situations and locations where it is most appropriate for installation.
Aluminum is often a preferred choice for coastal environments due to its resistance to rust in salty conditions.
Its lightweight nature and widespread availability make it convenient for installers to work with.
Additionally, there are various warranty options available for aluminum, such as a PVDF paint warranty for coastal and Caribbean regions.
However, it is important to note that aluminum can be more susceptible to dents, comes at a higher price compared to steel, and requires adequate space for thermal expansion.
Metal Roofing Experts is committed to providing valuable information to customers and potential buyers, allowing them to make well-informed decisions about the most suitable metal material for their roofing project, whether it be aluminum or another option. We are able to collaborate with a variety of professionals, including contractors, architects, manufacturers, and property owners, to assist in selecting the best material for their specific projects.
Please reach out to one of our experienced metal roofing specialists today with any questions you may have about aluminum or other types of metal roofs!